Comparison of Electromechanical and Hydraulic Guillotines
A guillotine is recognized as a powerful cutting machine in various industries. This device is used for precise and efficient cutting of different materials, including metals, plastics, paper, and more. Guillotines are widely utilized in metalworking, printing, packaging, and parts manufacturing industries due to their high precision and ability to make quick, clean cuts. Depending on the type and thickness of the material, guillotines are produced in various sizes and power levels, each suitable for specific applications.
The Importance of Choosing the Right Guillotine Based on Industrial Needs
Selecting the appropriate guillotine can significantly impact the efficiency and quality of industrial processes. In industries where cutting precision and the final product quality are critical, choosing a guillotine with the correct technical specifications becomes particularly important. Factors such as the type of material to be cut, its thickness, the required cutting speed, and maintenance and operational costs are all essential considerations when selecting a guillotine. An incorrect choice may result in reduced productivity, increased costs, and even frequent breakdowns.
Introduction to the Two Main Types of Guillotines: Electromechanical and Hydraulic
Guillotines are divided into two main categories: electromechanical guillotines and hydraulic guillotines.
- Electromechanical Guillotine: This type of guillotine uses electric motors to drive the blades. Electromechanical guillotines are popular for their high precision and ease of control in performing precise and lighter cuts. They are particularly useful in industries such as printing and packaging, where precise cuts are essential. Lower maintenance and operating costs are additional advantages of this type of guillotine.
- Hydraulic Guillotine: This guillotine type uses hydraulic fluid pressure to apply cutting force. Hydraulic guillotines are known for their high cutting power, making them suitable for heavy-duty industries like metalworking and construction. Due to their strong cutting capabilities, these machines are ideal for heavy and continuous applications. However, maintaining these machines requires greater attention due to the complexity of the hydraulic system.
Introduction to Guillotine Cutting Machines
Definition of Guillotine: A guillotine, as an industrial cutting tool, utilizes a sharp and powerful blade to cut various materials. This machine is commonly used to cut metal sheets, plastics, paper, and even some harder materials in diverse industries. The guillotine operates on the principle of a blade moving downward through specific mechanisms to apply high pressure and split the material into two parts. This cutting process, known for its precision and speed, makes the guillotine an essential tool in production lines.
Guillotines are manufactured in various sizes and power capacities, with different types suited for specific materials and applications. Some guillotines are specially designed for cutting thin and delicate materials, while others are used for thicker and harder materials. As a result, guillotines find extensive use in industries such as metalworking, printing, packaging, construction, and even in artisanal crafts.
History of the Guillotine: From Traditional Models to Today’s Advanced Versions
The history of the guillotine dates back to the Industrial Revolution in Europe, a period when the need for tools to increase speed and accuracy in industrial production became more critical. The earliest guillotines were simple, manually-operated machines designed for cutting paper and fabric, relying heavily on the physical strength of the operators.
As technology progressed, guillotines evolved into more advanced machines. In the 19th century, with the introduction of industrial machinery to production lines, mechanical guillotines replaced manual models. These machines used more complex mechanical mechanisms to exert cutting force and were capable of cutting harder, thicker materials with greater precision.
With the advent of new technologies in the 20th century, electromechanical and hydraulic guillotines emerged. Electromechanical guillotines use electric motors to drive the blades, providing high precision and enhanced control over the cutting process, making them suitable for many industries. Hydraulic guillotines, on the other hand, apply greater cutting force through hydraulic pressure, making them ideal for cutting hard and thick materials.
Role of Guillotines in Industry: Applications in Sectors like Metalworking, Printing, and Packaging
Due to their diverse and versatile capabilities, guillotines play a vital role across various industries. One of their primary applications is in the metalworking industry, where guillotines are used for precise cutting of metal sheets. The accuracy and speed of these machines enhance the quality of metal parts production. Hydraulic guillotines are especially popular in this field because of their ability to cut thick, hard sheets.
In the printing industry, guillotines are used for precise cutting of paper and cardboard. Electromechanical guillotines, known for their high precision and fine adjustment capabilities, are widely used in this sector. These machines can cut paper sheets at high speeds without causing damage or defects, producing sheets to exact sizes.
The packaging industry also heavily relies on guillotines, where they are used to cut packaging materials such as plastic, paper, and metal foils. Electromechanical guillotines, with their high accuracy and broad adjustment capabilities, are particularly beneficial for precise and clean cuts in packaging production.
Guillotines are also utilized in other sectors, including construction, food industries, and even crafts. In each of these fields, choosing the right type of guillotine based on the material type and specific application is crucial for improving efficiency and the final product quality.
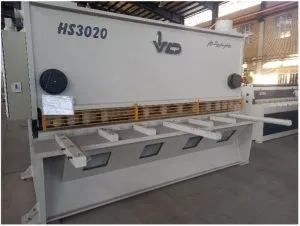
Electromechanical Guillotine
Operating Mechanism
Electromechanical guillotines use electric motors to drive cutting blades, functioning through a blend of mechanical and electrical technology. The electric motors provide the power needed to move the blades, and the mechanical mechanisms within these devices transfer this force to the blades. This mechanism allows electromechanical guillotines to make precise cuts at high speeds.
One of the key features of electromechanical guillotines is their high precision in cut settings. Users can adjust the depth and angle of the cut with great accuracy, making these machines highly suitable for industries that require precise and uniform cuts, such as printing and packaging.
Advantages and Disadvantages
Electromechanical guillotines offer numerous advantages, making them ideal for various industries. One of the most significant benefits is their high accuracy and precise control over the cutting process. These guillotines can perform extremely accurate cuts with minimal error.
Other advantages include easier maintenance and lower operational costs. Thanks to their simpler mechanical and electrical systems, these machines require less maintenance and, compared to hydraulic guillotines, incur lower operational costs.
However, electromechanical guillotines may have limitations when cutting very hard or thick materials. These machines generally exert less cutting force than hydraulic guillotines and may not be as effective for cutting very thick or rigid materials.
Applications
Electromechanical guillotines are widely used in industries requiring quick, precise cuts. In the printing industry, they are used for accurate cutting of paper and cardboard. In the packaging industry, electromechanical guillotines are applied to precisely cut packaging materials such as plastic and metal foils. They are also used in the electronics industry for the precise cutting of electronic components and printed circuits.
Maintenance and Repairs
Due to their simpler structure, electromechanical guillotines require less maintenance. Regular inspections, proper lubrication, and routine cleaning of internal components can significantly extend their lifespan. Additionally, replacing worn parts, such as blades and moving mechanisms, at regular intervals can help improve performance and increase the machine’s longevity.
Hydraulic Guillotine
Operating Mechanism
Hydraulic guillotines utilize hydraulic fluid pressure to move the cutting blades. These machines operate through complex hydraulic systems capable of generating substantial cutting force. In these systems, a hydraulic pump pressurizes the hydraulic fluid, which is then directly transmitted to the cylinders and blades. This mechanism enables hydraulic guillotines to cut through very thick and hard materials with significant power and precision.
A unique feature of hydraulic guillotines is their ability to apply consistent force throughout the entire cutting process. This ensures flawless cuts, providing precisely and evenly cut pieces. Additionally, these machines can perform continuous cuts at high speed without interruption.
Advantages and Disadvantages
Hydraulic guillotines offer several advantages, making them ideal for cutting thick and tough materials. One of the most notable benefits is their high cutting power, which enables them to slice through very thick and hard materials—an essential capability for heavy industries like metalworking.
Other advantages include smooth performance and continuous cutting capability. Due to their advanced hydraulic systems, these machines can execute highly precise and uniform cuts while maintaining continuous operation without pausing.
However, hydraulic guillotines require more maintenance, and their operating costs are higher compared to electromechanical guillotines. Due to the complexity of their hydraulic systems, these machines need regular servicing and inspections, and any fault or breakdown in the hydraulic system can lead to a complete halt in operation.
Applications
Hydraulic guillotines are widely used in industries requiring the cutting of thick and tough materials. These machines are especially valuable in the metalworking industry for cutting thick metal sheets, manufacturing automotive parts, and construction work. Furthermore, hydraulic guillotines are practical in industries that demand continuous heavy-duty cutting, such as large-scale manufacturing and industrial production facilities.
Performance Comparison
The performance of electromechanical and hydraulic guillotines varies depending on the specific industrial needs. Hydraulic guillotines are more suitable for heavy-duty and continuous applications due to their high cutting capacity for thick and hard materials. These machines are especially useful in industries that require high power and consistent cuts.
On the other hand, electromechanical guillotines are more suitable for applications requiring precise and fast cuts due to their high accuracy and better control over the cutting process. These machines are particularly useful in industries that need to cut thinner and more sensitive materials, such as printing and packaging.
Cost Comparison
The purchase and maintenance costs of hydraulic guillotines are generally higher. These machines, due to the use of complex hydraulic systems, require more regular servicing and inspections, and any malfunction or failure in the hydraulic system can result in high costs. On the other hand, electromechanical guillotines, with their simpler structure, require less maintenance, and their operational costs are lower.
Comparison in Industrial Applications
For industries that need precise and fast cuts, electromechanical guillotines are a better choice. These machines, due to their high accuracy and control over the cutting process, can perform precise cuts with minimal errors. On the other hand, industries dealing with thick and hard materials that require high cutting power will find hydraulic guillotines more suitable. These machines, due to their high power for cutting hard and thick materials, are better suited for heavy-duty and continuous applications.
Important Points in Choosing the Right Guillotine
Assessing Specific Needs: How to Evaluate Your Specific Requirements
Choosing the right guillotine for any business or factory requires a clear understanding of the specific needs of the industry. The first step in this process is evaluating your specific needs, which includes the following:
- Type of Material to Be Cut: The type of material to be cut with the guillotine is crucial. For example, if you are cutting heavy and thick metals, you need a guillotine with high power and capacity, such as a hydraulic guillotine. However, if you are cutting thinner and more precise materials like paper or plastic, an electromechanical guillotine would be a better choice.
- Production Volume: If your production volume is high and requires continuous and consistent cutting, a hydraulic guillotine is the better choice due to its ability to handle heavy and continuous cuts. However, if you need precise cuts with lower volumes, an electromechanical guillotine would be more suitable due to its higher accuracy and lower maintenance needs.
- Cutting Accuracy: In industries where cutting accuracy is highly important, such as printing and packaging, electromechanical guillotines are preferred due to their better control and higher precision. These machines allow for precise cutting adjustments, making them very useful for cutting sensitive materials.
- Budget: Evaluating the available budget for purchasing a guillotine also plays an important role in selecting the right machine. Hydraulic guillotines are generally more expensive and require more maintenance, but they are more cost-effective for heavy-duty and continuous applications. Electromechanical guillotines are less expensive and are more suitable for precise and lighter applications.
Purchasing Advice: Guidance for Buying the Best Guillotine Based on Budget and Work Needs
Purchasing a guillotine is an important investment for any factory or production workshop. Here are some key tips to help you choose the best guillotine based on your budget and work needs:
- Consultation with Experts: Before making a final decision, it is recommended to consult with industry experts and specialists. They can guide you in selecting the best guillotine based on your specific needs.
- Visiting Manufacturers and Sales Representatives: Visiting manufacturing plants and guillotine sales representatives can help you familiarize yourself with various types of machines and their features. Additionally, you may be able to see the machines in action and get a closer look at their performance.
- Checking Warranty and After-Sales Service: Make sure there is a valid warranty and after-sales service. This ensures that if any issues arise, you can resolve them quickly and prevent production stoppage.
- Comparing Prices and Features: Before purchasing, compare the prices and features of different machines. This will help you select a guillotine that fits within your budget while meeting your work requirements.
Safety Tips: Safety Guidelines for Using Guillotines
Using guillotines requires strict adherence to safety guidelines due to their high cutting power and ability. Here are some important safety tips:
- Training Users: All operators who use the guillotine should be fully trained. This training should include proper machine usage, recognizing potential hazards, and methods for avoiding them.
- Using Protective Equipment: Operators should always use protective equipment such as gloves, safety glasses, and ear protection to prevent potential injuries.
- Installing Safety Guards and Systems: Guillotines should be equipped with safety guards and systems such as emergency locks, automatic stop sensors, and blade guards. These features prevent accidents and ensure safe operation.
- Regular Inspection and Maintenance: Guillotines should be regularly inspected and maintained to ensure safe and proper performance. Regular checks of the blades, hydraulic and electrical systems, and other machine components are essential.
- Following Manufacturer’s Instructions: Always follow the manufacturer’s instructions and guidelines. These manuals provide detailed information on how to use the machine correctly, maintain it, and perform periodic servicing.
Innovations and New Technologies in Guillotines
Smart Guillotines: Introduction to Smart Guillotines with Automation Capabilities
With advancements in technology, guillotines have also undergone significant transformations, and now smart guillotines with automation capabilities are available in the market. These guillotines are equipped with intelligent systems and digital controls that allow precise and automatic adjustments of cutting parameters.
- Digital Control Systems: Smart guillotines use digital control systems that allow precise and automatic adjustments of the cutting settings. These systems allow users to easily enter their required parameters, and the machine automatically applies the necessary adjustments.
- Smart Sensors: Advanced sensors in smart guillotines can automatically detect the material thickness and adjust the cutting settings accordingly. This feature improves accuracy and reduces waste.
- Network Connectivity and Remote Control: Some smart guillotines have network connectivity and remote control features. This allows production managers to monitor and control the machines remotely, optimizing their performance.
- Data Recording and Analysis: Smart guillotines can record and analyze data related to the cutting process. These data can help improve efficiency and reduce costs, as users can make better decisions based on this information.
New Technologies: Reviewing the Latest Technologies in Electromechanical and Hydraulic Guillotines
In recent years, new technologies have been added to both electromechanical and hydraulic guillotines, improving the performance of these machines. Here are some of these technologies:
- Powerful Motors with Low Energy Consumption: One of the recent innovations in electromechanical guillotines is the use of powerful electric motors with low energy consumption. These new motors have greater cutting ability for thick materials while consuming less energy, which helps reduce operational costs.
- Advanced Hydraulic Systems: New hydraulic guillotines are equipped with more advanced hydraulic systems capable of generating greater cutting force with higher accuracy. These systems also reduce the need for frequent maintenance and increase the longevity of the machine.
- Adjustable and Quick-Change Blades: New technologies in guillotine blade designs have focused on making blades adjustable and easily changeable. This allows users to easily replace blades and perform various cuts with high precision.
- Use of Advanced Materials for Blade Construction: Modern guillotine blades are made from advanced materials such as tungsten carbide, which have longer lifespans and better cutting abilities for harder materials.
- Advanced Cooling Systems: Modern guillotines are equipped with advanced cooling systems that prevent the blades and the machine from overheating. These systems improve machine performance and increase its lifespan.
In this article, we have thoroughly reviewed guillotines, from their history and definition to important points in choosing and purchasing these machines. Guillotines play a crucial role in improving the efficiency and quality of manufacturing processes across various industries.
Electromechanical and hydraulic guillotines each have their own advantages and disadvantages. Electromechanical guillotines, due to their high precision and lower maintenance costs, are more suitable for industries requiring precise and fast cuts. On the other hand, hydraulic guillotines, with their high power and ability to cut thick and hard materials, are better for heavy-duty and continuous applications.
Innovations and new technologies in guillotines have also played a significant role in enhancing their performance and increasing their efficiency. From smart guillotines with automation capabilities to new technologies in electric motors and hydraulic systems, all these advancements have made guillotines more advanced and efficient.
Ultimately, selecting the right guillotine depends on your specific industrial needs. By carefully evaluating your needs, consulting with experts, and considering safety tips, you can choose the best guillotine for your business and benefit from the numerous advantages these machines offer in improving the efficiency and quality of your production.