To transform metals, predominantly steel and iron, into components and products, we require cutting. Cutting, especially of iron sheets, is one of the most common and widely used manufacturing processes. In this process, the metal sheet or any metal shape is cut, excess parts are removed, and the remaining piece is sized for subsequent use. The cut sheet can then be bent into the desired shape using a hydraulic press brake or a hydraulic full-bend press, or it can be transformed into desired shapes using high-volume hydraulic or mechanical presses, punches, and molds. However, cutting is the starting point and the first step in the production of metal products.
For this purpose, various tools and machines such as gas cutting, plasma cutting, mechanical shears, hydraulic shears, laser cutting, and more are used.
Despite the existence of various cutting machines including laser cutting, plasma cutting, etc., mechanical and hydraulic shears still maintain their position and are widely used (especially in direct and linear cuts) due to their high speed, easy machine maintenance, ease of use, and more. Large-scale machine manufacturing proudly produces powerful hydraulic shears in two types: guillotine and swing beam. The hydraulic shears produced by Large Machine Manufacturing use high-quality raw materials (in structure, blades, jacks, motors, etc.), are highly durable, and can be used for cutting iron and steel sheets in various dimensions and thicknesses (depending on the requirements of valued customers).
Introduction to Hydraulic Guillotine Shear Manufactured Dayyani Grand Machine Manufacturing
The hydraulic guillotine shear manufactured by Large Machine Manufacturing consists of the following components:
1. Body (Main Structure):
The main part of the device is the body, which is the part you see the device in. All components of the device are located on the body. Therefore, it is important that the structure of the device has the necessary strength and power for the cutting process. The force generated by the pressure of the jacks is exerted on the entire structure and body, so it is very important that the body does not bend or twist under this pressure. Any deformation, even in sizes of tenths of a millimeter, affects the quality of the cut. Therefore, the use of high-quality raw materials, accurate calculations of the body shape, appropriate thicknesses of base plates, table, and jaws of the machine in a way that, while avoiding unnecessary weight, can withstand the incoming forces, and the use of suitable stabilizers in different areas of the body, etc., are very important and play a crucial role in the final cutting quality. Large Machine Manufacturing has been producing and supplying high-quality and durable hydraulic guillotine shears for years by using experienced designers and modeling from first-class European machines. The high quality of the produced guillotine shears is evident from the fact that hydraulic shears with a lifespan of over 30 years produced by Large Machine Manufacturing are still used in Iran, the Middle East, North Africa, and other parts of the world.

Introduction to Hydraulic Guillotine Shear Manufactured by Dayyani Grand Machine Manufacturing
The hydraulic guillotine shear manufactured by Dayyani Grand Machine Manufacturing is composed of the following components:
Blades:
The cutting process is carried out by two blades, one of which (the lower blade) is fixed, and the other (the upper blade) is movable, and the workpiece is placed between these two blades. The lower blade is fixed on the table, and the upper blade is mounted on the jaws of the machine and, due to the force generated by the jacks and the movement of the jaws downwards towards the workpiece, approaches the workpiece. Due to the pre-determined distance between the blades, the cutting operation is performed. It is obvious that the quality and durability of the blades depend entirely on the material of the blades. Therefore, Large Machine Manufacturing uses the best raw materials available in the market to manufacture the blades. The blades are first machined, and then heat treatment processes are performed to achieve the desired strength. Finally, to remove any burrs and distortions in the blades, grinding operations are performed by a magnetic grinding machine to provide the highest level of quality.
Jacks:
Jacks are responsible for producing the force required to move the jaws and perform the cutting process. The power of the jacks must be such that no defects occur in cutting sheets with maximum length and thickness. Smooth and reproducible cutting results from the appropriate power of the jacks. At Large Machine Manufacturing, we assure our valued customers that the power of the jacks conforms to what is declared by the company, and you can enjoy cutting raw materials for many years with peace of mind.
The jacks manufactured by Large Machine Manufacturing are the result of the efforts and design of the company’s skilled experts and provide the necessary force for cutting sheets from 2 meters to 7 meters in length and from 6 millimeters to 30 millimeters in thickness (and even higher depending on the needs of the customers).
Motor, Pump, and Hydraulic System:
Powerful and high-quality motors and pumps are used for the movement of fluid (oil) in the hydraulic system of the machine. The hydraulic system design of the machines is carried out by experienced specialists at Large Machine Manufacturing and is highly efficient and powerful. The electrical connections, valves, etc., used in the hydraulic guillotine shears of Large Machine Manufacturing are made of selected quality materials and provide you with peace of mind for years.
Accumulator:
To save energy, an accumulator system is used in the hydraulic guillotine shears manufactured by Dayyani Grand Machine Manufacturing. The accumulator system stores energy when the jaws of the machine descend and uses it to lift the jaws. In this mode, the oil circulation and hydraulic system are disconnected, preventing the hydraulic oil from overheating and avoiding pressure buildup in the hydraulic system during long and continuous operation of the machine. This system increases the lifespan of the machine and saves energy consumption.
Back Gauge System:
As mentioned earlier, hydraulic guillotine shears manufactured by Dayyani Grand Machine Manufacturing are produced in two types: guillotine and swing beam. In the guillotine type, the back gauge is driven by a motor, gearbox, and chain. By adjusting the back gauge, you can set the desired cutting width. The movement of the back gauge in this type of product is only horizontal and moves in a linear motion.
In hydraulic swing beam guillotine shears, in addition to horizontal movement, the back gauge also moves vertically, and the back gauge system is disconnected from the circuit for ease of removing sheets or cutting with large widths. The force required for this movement is provided by the hydraulic system of the machine.
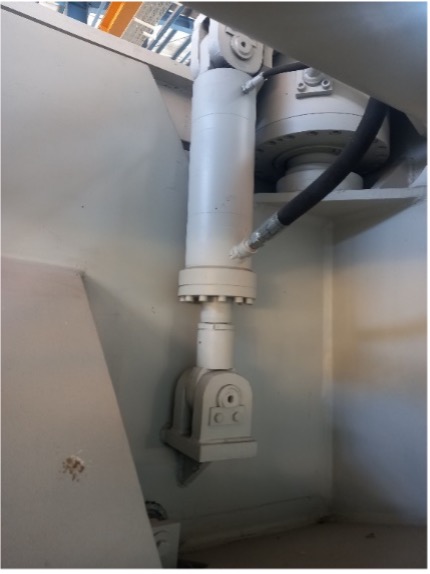
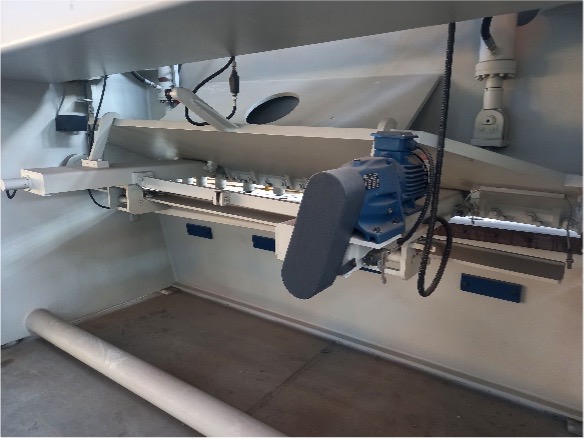
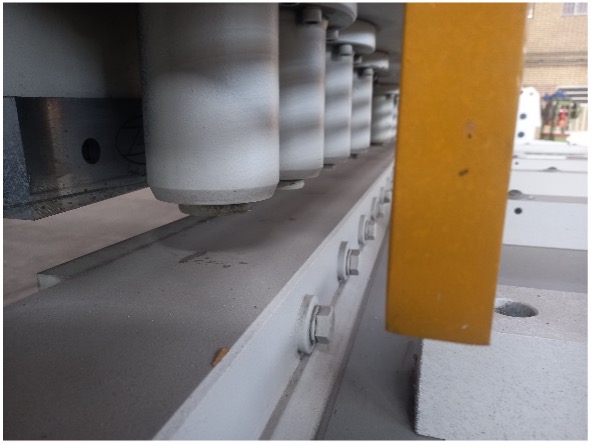
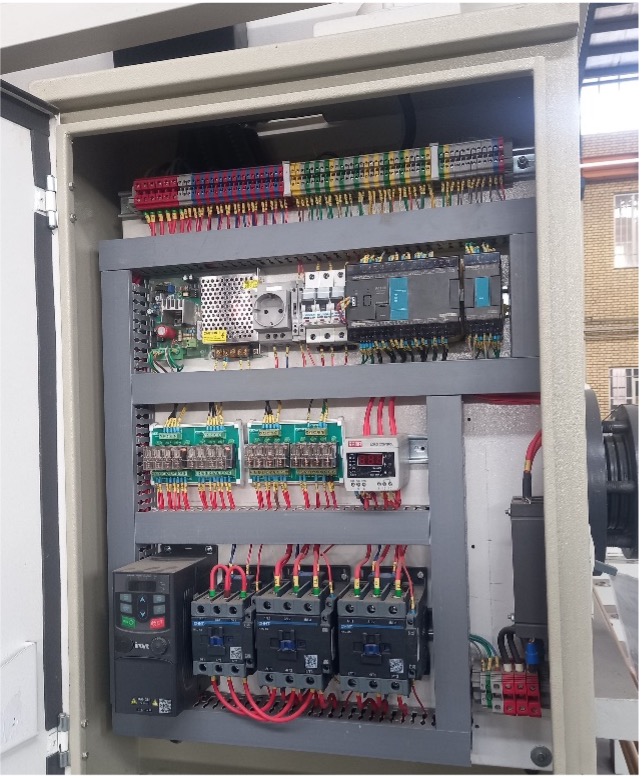

Sheet Holders:
To secure the sheet on the table of the guillotine, hydraulic sheet holders are installed in the hydraulic guillotine shears manufactured by Large Machine Manufacturing. The number of sheet holders ranges from 10 to 28 depending on the size of the machine, and they are connected to the central hydraulic system of the machine.
Control Panel and PLC of the Machine:
For ease of use, a PLC system is installed on the control panel of the machine. The PLC system facilitates control and adjustment of the cutting settings, allowing users to easily apply their desired settings to the machine.
Machine Controller:
The hydraulic guillotine shears manufactured by Dayyani Grand Machine Manufacturing are equipped with a PLC system that allows adjustment of the blade gap and angle based on the thickness of the sheet. Therefore, the user enters all the specifications of the sheet, including thickness, cutting length, etc., and adjusts the machine’s pressure and other required cutting parameters accordingly.
Technical Specifications and Parameters of Hydraulic Guillotines Manufactured by Dayyani Grand Machine Manufacturing
In the table below, you can see various models of hydraulic guillotines (both swing beam and guillotine) along with their technical specifications. This table can serve as a useful guide for selecting the best hydraulic guillotine machine that suits your needs.
| Model | Cutting Length (mm) | Cutting Thickness (mm) | Cutting Angle (°) | Back Gauge Range (mm) | Motor Power (kW) | Weight (kg) |
|—————-|———————|————————|——————–|———————–|——————|————-|
| Model A | 2500 | 6 | 1.5 | 600 | 7.5 | 4500 |
| Model B | 3200 | 8 | 1.8 | 800 | 11 | 6200 |
| Model C | 4000 | 10 | 2.0 | 1000 | 15 | 8000 |
| Model D | 5000 | 12 | 2.5 | 1200 | 18.5 | 10000 |
| Model E | 6000 | 16 | 3.0 | 1500 | 22 | 13000 |
These specifications provide valuable information regarding the cutting capacity, dimensions, and power requirements of each hydraulic guillotine model, aiding in the selection process based on specific operational requirements.
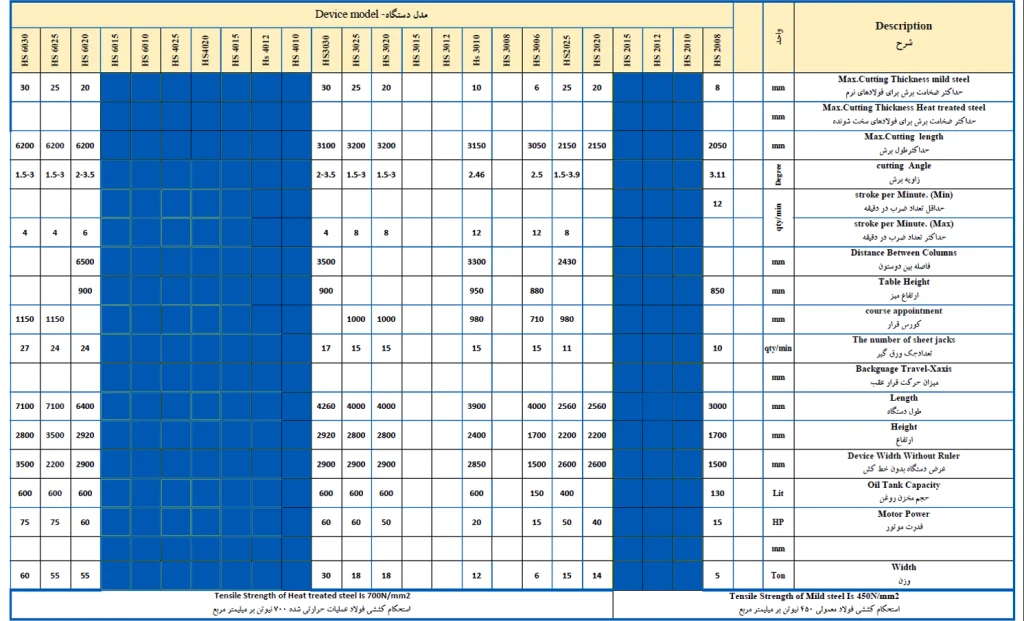
Advantages of Hydraulic Guillotines Manufactured by Dayyani Grand Machine Manufacturing:
1. Cutting Power for Thick Sheets: Capable of cutting sheets up to 50 millimeters thick.
2. Wide Operating Range: Ability to cut various metal sheets with cutting lengths ranging from 1 to 7 meters.
3. Good Operational Speed Alongside Suitable Cutting Quality: Provides a good balance between operational speed and cutting quality, minimizing burrs and maximizing cutting smoothness.
4. Adjustable Cutting Angle (Swing Beam Models): The cutting angle can be adjusted according to requirements.
5. Long Blade Lifespan Due to the Use of High-Quality Steels: Ensures durability and longevity of cutting blades.
6. High Power and Durability of Holding Jacks, Cylinders, and Hydraulic System: Ensures reliable performance under heavy-duty operations.
7. Utilization of Accumulator System: Energy-efficient operation and reduced wear and tear on the hydraulic system.
8. Unlimited After-Sales Services and Spare Parts Supply by Dayyani Grand Machine Manufacturing: Ensures continuous support and maintenance services for the equipment.